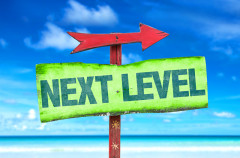
Mit Retrofitting lässt sich die nächste Stufe in der Unternehmensentwicklung erreichen.
© Panthermedia
Analoge Säge wird smart
Die Firma Hedemann Technik digitalisert mit Hilfe des Mittelstand 4.0-Kompetenzzentrums eine alte Maschine, lernt viel und spart dabei auch noch. Ein Leuchtturmprojekt aus der Abteilung „Retrofitting“.
Dirk Leenderts steht in der Werkstatt. Der Geschäftsführer der Westersteder Hedemann Technik GmbH blickt auf viel Tradition und gleichzeitig sieht er jede Menge Zukunft. Der zertifizierte Schweißfachbetrieb ist seit über 125 Jahren in der Agrarwirtschaft tätig. Die Firma beliefert Kunden aus der Landwirtschaft und der Lebensmittel- und Tierfutterindustrie. Die Bandsäge, auf die Leenderts zusteuert, ist knapp 25 Jahre alt. Sie dient dem Zuschnitt von Bauteilen im Rahmen der Fertigung. Das Problem: Die Maschine besitzt keinerlei digitale Schnittstellen zur Einbindung in die Softwarelandschaft des Unternehmens. „Ein Neukauf würde eine Ausgabe von 9500 Euro bedeuten“, sagt der Chef von 44 Mitarbeitern. „Als ich von Retrofitting gelesen habe, bin ich hellhörig geworden.“
Kay Lutz Pakula, Beauftragter für Innovation und Technologie (BIT)* bei der Handwerkskammer Oldenburg, erklärt: „Retrofitting bedeutet alte Maschinen nachzurüsten, das heißt speziell in unserem Fall: sie werden smart gemacht. Mithilfe von beispielsweise Sensoren können so wie bei neuen Maschinen Daten erfasst werden, die für Kosten- oder Verfügbarkeitsbetrachtungen heutzutage erforderlich sind.“ Pakula organisierte im Februar mit dem Mittelstandszentrum einen Workshop zum Thema. Dabei ließ sich Dirk Leenderts inspirieren.
Bei Hedemann in Westerstede sieht die Lage nämlich wie folgt aus: Die Metallbearbeitung erfolgt über eine CNC-Plasmaschneidanlage, eine CNC-Abkantpresse sowie über Bandsägen für den Profilzuschnitt. Zur Steigerung der Transparenz in der Produktion möchte das Unternehmen die Chancen der Digitalisierung nutzen. Die hierzu erforderlichen Rückmeldedaten stehen jedoch aktuell nicht zur Verfügung, sodass die Verfügbarkeit der Maschine nur mit einem hohen manuellen Aufwand erfasst werden kann.
Sensorkonzept für die Datenerfassung
Der Seminarleiter des Workshops war Dr. Michael Rehe. Der Geschäftsführer vom Mittelstand 4.0-Kompetenzzentrum Hannover schlug der Firma Hedemann daraufhin ein Leuchtturmprojekt in der Produktion vor. Zielsetzung: Die Verfügbarkeit der Bandsäge in Echtzeit zu berechnen und über ein Endgerät zu visualisieren. Die Kosten für die Sensorik zahlt der Betrieb, der Rest wird über das Kompetenzzentrum finanziert.
„Daten aus der Produktion sind die Grundlage zur Steigerung der Effizienz und Wirtschaftlichkeit“, sagt Rehe. Die Landmaschinenmechaniker und Metallbauer der Firma Hedemann können sich diese Daten demnächst zunutze machen. Michael Rehe erklärt: „Basierend auf den Anforderungen der Firma Hedemann hat das Kompetenzzentrum Hannover ein Sensorkonzept für die Datenerfassung erstellt und prototypisch umgesetzt.
Auf dieser Grundlage erfolgt die Ermittlung der Betriebszustände, die über eine Anwenderoberfläche dargestellt werden. Mittelfristig sollen die Mitarbeiter das System eigenständig weiterentwickeln.“ Daher erfolgt die Programmierung dieser Anwendung mittels LowCode. „Sie kann mit geringem Schulungsaufwand erlernt werden“, blickt Dirk Leenderts voraus. Zurzeit wird die Sensorik nach ersten Tests feinjustiert.
Geschäftsführer Leenderts freut sich auf den Einsatz und ist begeistert vom Prinzip „Retrofitting“. Er sieht ganz viel Potenzial für zahlreiche Betriebe. In sein Unternehmen passe „Retrofitting“ auf jeden Fall - zwischen den Blicken auf die Tradition einerseits, und denjenigen in die Zukunft andererseits.
Mehr zum Unternehmen: hedemann-technik.de
* Gefördert durch das Bundesministerium für Wirtschaft und Technologie aufgrund eines Beschlusses des Deutschen Bundestages
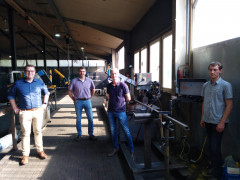
Dirk Leenderts (li.) mit Besuch (weiter v. li.): Kay Lutz Pakula (Handwerkskammer), Dr. Michael Rehe (Mittelstand 4.0-Kompetenzzentrum Hannover) und Tobias Hein (studentische Hilfskraft im Projekt).
© Hedemann